Meating the challenge to optimise lamb
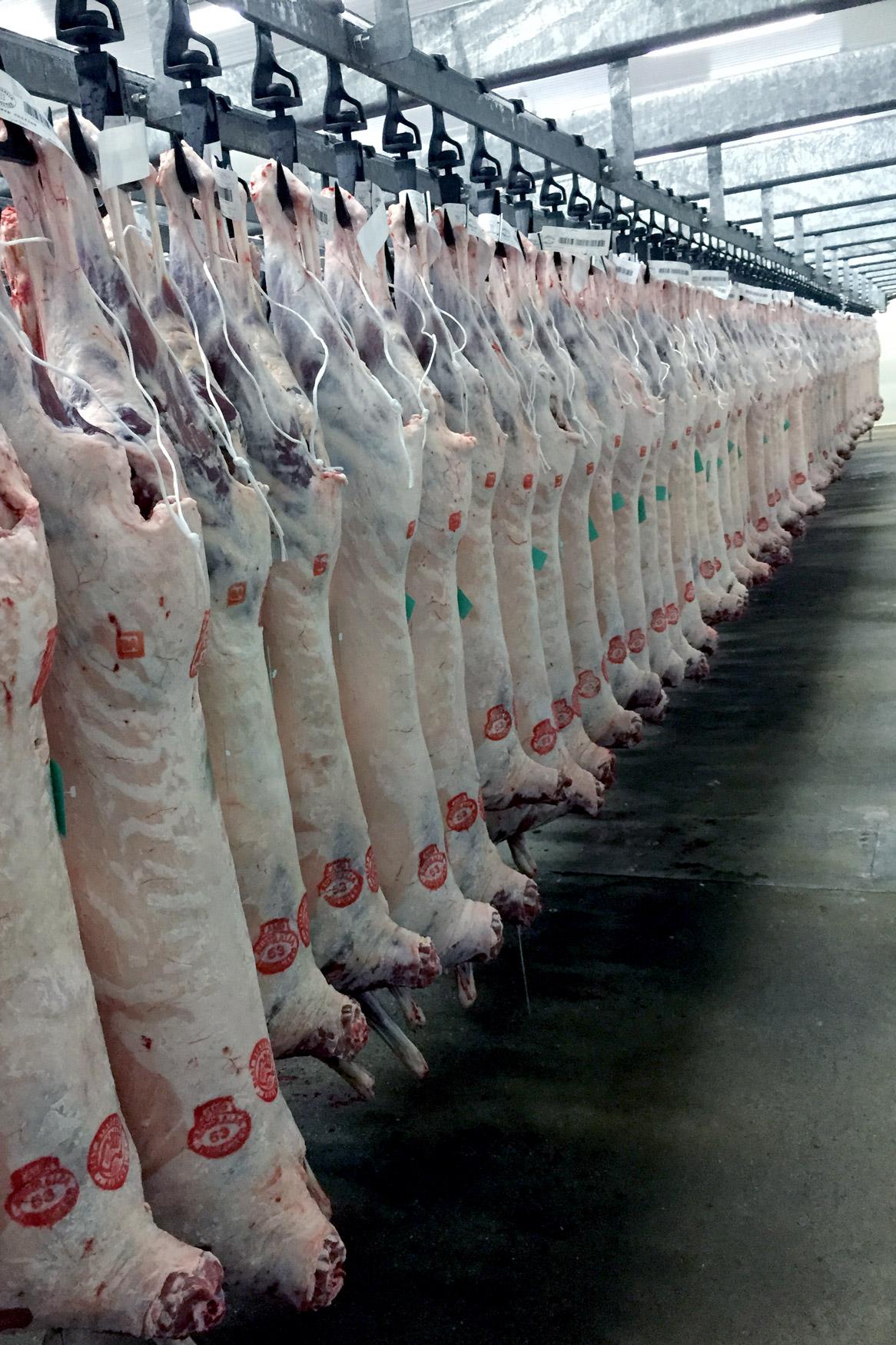
Case study: When profit margins are small, businesses look to innovate to find the one-percenters that can make the difference between success and failure.
In the red meat processing industry innovation opportunities are emerging with a new generation of carcase measurement technology that significantly increases the precision and accuracy of yield prediction of lamb carcases.
With this information at hand, lamb processors can now turn to the power of mathematics and employ optimisation methodologies to guide them to make the most from each carcase.
The development of a Lamb Carcase Optimisation Tool has been a journey of discovery through a multi-disciplinary collaboration led by Davies Livestock Centre’s Director and Program Leader of the Advanced Livestock Measurement Technologies project (ALMTech), Professor Wayne Pitchford, the University’s Teletraffic Research Centre, researchers from Murdoch University, and commercial partners Agbiz Solutions and Gundagai Meat Processors (GMP).
For ALMTech Research Fellow, Dr Sean Miller, bringing all involved in the project together to develop an understanding of the problem at the outset has been a critical success factor.
“Everyone from the meat science research team to the mathematicians and red meat processing partners has had to share and learn each other’s language to enable the platform to be built,” Dr Miller says.
“Without this basic understanding of how lamb processing works, and how the mechanics of meat fabrication can be coded mathematically, it would have been unachievable to develop a tool that is credible to industry.”
Lamb processing company GMP’s Client Research Adviser, Dr Michelle Henry says, “the objective of optimisation is to select the right carcase for the right cut.”
Using the ALMTech Lamb Carcase Optimisation Tool, GMP can begin to compare the impact on the profitability of the business of fabricating lamb carcases to a range of different specifications, and empower them with the ability to improve the decision they make on a day to day basis.

Dr Andre Costa, Director of the University’s Teletraffic Research Centre, says that it was “important that we took a systematic approach; starting simple and validating our understanding of the outputs at each step.”
This has been helping the team develop an appreciation of the variability associated with predictions of profit as carcase fabrication decisions are changed, and the scale of improved profit, both positive and negative, that may result.
And like all involved in the project, Andre sums it up best when he says “We are very keen to see this succeed”!
By Sean Miller